在石油化工領域,從原油裂解到高附加值化學品合成,固定床實驗裝置正以毫米級催化劑床層和微秒級反應控制,重構著傳統化工生產的效率邊界。這種將固體催化劑精密填充于高壓反應器內的技術,已成為催化裂化、加氫精制、烷基化等核心工藝研發的“標準配置”。
一、催化裂化:重質油輕量化的“分子剪刀”
在固定床催化裂化實驗裝置中,直徑2-5mm的分子篩催化劑顆粒形成三維孔道網絡,使重質油分子在450-550℃高溫下發生定向斷裂。某煉化企業通過微型固定床反應器模擬實驗,發現采用ZSM-5分子篩催化劑時,汽油產率較傳統流化床提升8%,且烯烴含量降低12%。這種“實驗室-中試-工業裝置”的三級放大模式,使新催化劑研發周期從3年縮短至18個月。
二、加氫精制:油品清潔化的“分子凈化器”
固定床加氫實驗裝置通過精確控制氫氣分壓(5-20MPa)和反應溫度(300-450℃),實現硫、氮、金屬等雜質的高效脫除。在柴油加氫脫硫實驗中,采用NiMo/Al2O3催化劑的固定床反應器,可將硫含量從5000ppm降至10ppm以下,同時保持十六烷值提升3-5個單位。某科研機構開發的梯度孔催化劑,在固定床實驗裝置中驗證了其抗積碳性能,使加氫裝置運行周期延長40%。
三、烷基化:清潔汽油組分的“分子拼接師”
在異丁烷與烯烴的烷基化反應中,該實驗裝置通過優化催化劑裝填方式(如徑向床層設計),使反應選擇性突破90%。某企業采用磺酸基離子交換樹脂催化劑的固定床反應器,生產的烷基化油辛烷值達96,且烯烴含量低于1vol%,滿足國VI汽油標準。實驗數據顯示,該裝置單位催化劑處理量較釜式反應器提升5倍,催化劑壽命延長至2年以上。
四、工藝放大:從實驗室到工業化的“橋梁”
固定床實驗裝置的模塊化設計(如可拆卸式加熱爐、快速換熱系統),使其能精準模擬工業裝置的流體力學特性。在某百萬噸級加氫裂化項目前期,通過1:100比例的固定床冷模實驗,優化了催化劑裝填密度和氣體分布器結構,使工業裝置壓降降低15%,年節能效益超千萬元。這種“微觀-宏觀”的跨尺度驗證能力,已成為新建化工項目風險控制的關鍵手段。
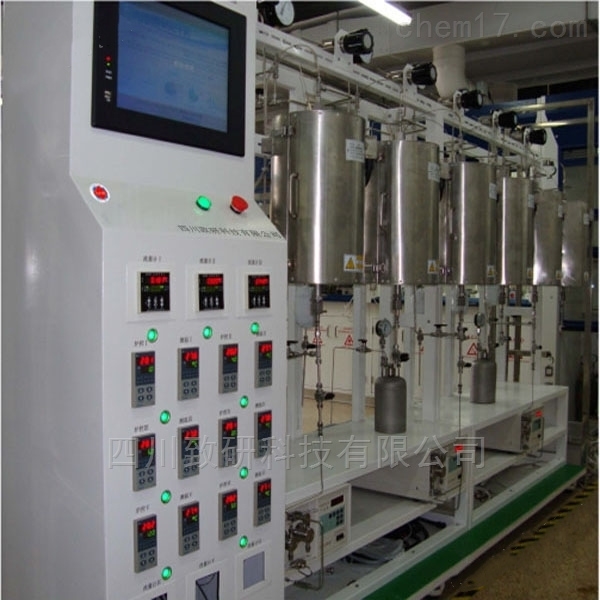
從分子級反應機理研究到萬噸級裝置工藝優化,固定床實驗裝置正以“精密手術刀”般的精準度,切割著石油化工產業升級的技術壁壘。隨著3D打印催化劑載體、AI反應條件優化等技術的融合,這一“微觀引擎”將持續推動行業向高效、清潔、智能的方向演進。